As an expert in Omron PLC and program controller products, I’ve gained a wealth of experience dealing with these highly sophisticated machines.
Over the years, I’ve tackled numerous challenges, giving me a unique insight into the common issues our clients face and how to resolve them.
Today, I want to share with you some of the most common Omron PLC error codes and the steps you can take to fix these issues.
1. Memory Error (Error Code: 80F1)
- Symptom: The PLC’s memory encounters an error, potentially leading to data corruption.
- Resolution: Check the PLC Setup and the memory allocation. If a checksum error is detected, you may need to reinitialize the memory and re-upload the program. In cases of hardware memory faults, the PLC unit may require replacement.
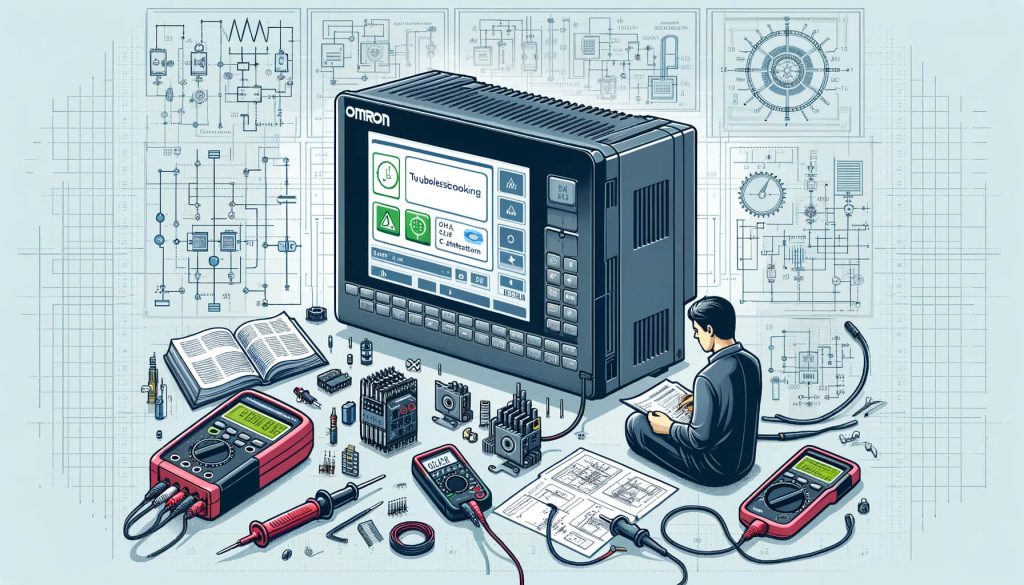
2. I/O Bus Error (Error Codes: 80C0 to 80CE, 80CF)
- Symptom: Communication issues between the CPU and I/O Units, leading to operational disruptions.
- Resolution: First, check and ensure that all connections and cables between I/O units and the CPU are secure. If the issue persists, inspect each I/O unit for malfunctions and replace if necessary.
3. Cycle Time Too Long (Error Code: 809F)
- Symptom: The cycle time of the PLC exceeds the maximum limit, causing delays in operations.
- Resolution: Optimize the PLC program to reduce cycle time. Consider dividing complex tasks and disabling unnecessary functions. In some cases, upgrading the PLC unit for better performance may be required.
4. Program Error (Error Code: 80F0)
- Symptom: The PLC detects an incorrect or corrupted program.
- Resolution: Check for program integrity. Ensure that there is an ‘END’ instruction at the end of the task. If the program has illegal instructions or addresses, correct these in the program and re-upload it to the PLC.
5. CPU Bus Error (Error Codes: 0200 to 020F)
- Symptom: Communication errors within the CPU Bus Units.
- Resolution: Inspect the CPU Bus Units for proper configuration and settings. Resetting the units or replacing any malfunctioning units may be necessary.
6. Battery Error (Error Code: 00F7)
- Symptom: The backup battery for the CPU unit is low, leading to potential data loss.
- Resolution: Replace the battery as soon as possible. Ensure that the PLC is powered during the replacement to prevent data loss.
7. Fatal System Errors (Error Codes: FAL(006), FALS(007))
- Symptom: The PLC encounters a critical system error, possibly halting operations.
- Resolution: These errors are often specific and require detailed diagnostics. Check the PLC manual for the specific FAL or FALS code and follow the recommended troubleshooting steps.
What is Error Code D9 on Omron CJ2M?
Error code D9 on the Omron CJ2M series often relates to issues in the communication or network settings. This error can arise due to incorrect network configuration, faulty connections, or issues with the communication units or cables.
How Do I Fix PLC Error?
To fix a PLC error, follow these general steps:
- Identify the Error: Check the PLC’s diagnostic lights or use a programming console to read the error code.
- Refer to the Manual: Each error code has specific meanings, often detailed in the PLC’s operation manual.
- Inspect Hardware: Look for physical signs of damage or wear on cables, units, and connectors.
- Review Program: For software-related errors, check the program for incorrect logic or instructions.
- Power Cycle: Sometimes, simply turning the PLC off and on can clear temporary glitches.
- Replace Faulty Components: If a hardware component is identified as faulty, replace it.
What is the Main Cause of PLC Failure?
PLC failures can be attributed to various factors:
- Electrical Issues: Power surges, short circuits, or unstable power supply can damage PLC components.
- Environmental Factors: Exposure to extreme temperatures, humidity, dust, or corrosive gases can affect PLC operations.
- Mechanical Stress: Vibration or physical impacts can disrupt connections or damage components.
- Software Glitches: Errors in programming or compatibility issues with connected devices can cause malfunctions.
- Aging Components: Over time, components like batteries, capacitors, and relays can wear out and fail.
How Do You Trace a Fault in a PLC?
Tracing a fault in a PLC involves a systematic approach:
- Start with Observations: Check indicator lights on the PLC and I/O modules. Blinking or unusual light patterns can indicate specific issues.
- Use Diagnostic Tools: Many PLCs have built-in diagnostics. Access these via the programming software to get detailed error information.
- Check I/O Status: Verify that each input and output is functioning correctly. A failed I/O point could be the source of the problem.
- Monitor the Program: Run the PLC program in a test mode, if available, to observe the behavior of different program blocks.
- Isolate the Issue: Disconnect parts of the system or replace components systematically to isolate the fault.
In conclusion, understanding and resolving these common error codes is crucial for maintaining the efficiency and reliability of your Omron PLC systems. Always refer to the official Omron operation manual for detailed guidance and consider reaching out to a professional if the issue persists.
For more detailed technical support on Omron PLCs, visit Omron’s Official Website or feel free to contact me at info@ikwoco.com.