However, like any sophisticated machinery, they are not immune to issues. Proper maintenance and timely troubleshooting are essential to ensure their longevity and efficient operation. This post aims to delve into the world of Omron PLCs, offering insights into their maintenance and troubleshooting, thus ensuring your operations run smoothly.
Understanding Omron PLCs
Overview of Omron PLC Types and Models
Omron offers a wide range of PLCs, catering to different industrial needs. From compact models perfect for small-scale applications to advanced systems designed for complex processes, understanding the specific type and model you are working with is crucial. Each model comes with its unique set of features and capabilities.
Key Features and Functionalities
Omron PLCs stand out for their user-friendly interfaces, robust performance, and adaptability. Key features often include high processing speeds, ample memory, diverse input/output options, and strong network capabilities. These features enable them to handle a variety of automation tasks with precision and efficiency.
Common Applications in Industry
These PLCs find applications across numerous sectors such as manufacturing, automotive, food and beverage, and pharmaceuticals. They are used for controlling machinery, assembly lines, robotic devices, and more, proving their versatility in different industrial settings.
Maintenance Tips for Omron PLCs
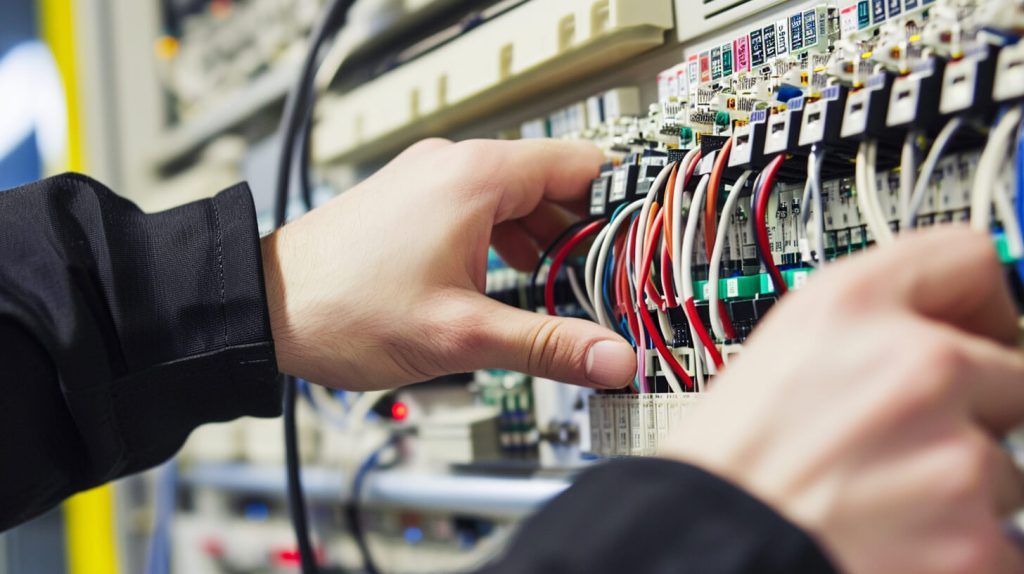
Regular Inspection
Routine checks are fundamental in maintaining the health of Omron PLCs. Regular inspections help in early detection of potential issues, preventing downtime.
- Visual Inspection for Physical Damages: Check for any signs of wear and tear, loose components, or damage.
- Checking Connections and Wiring: Ensure all connections are secure and wiring is intact, as loose or damaged wires can lead to malfunctions.
Software Updates and Backups
Keeping the PLC software updated is vital for security and efficiency. Regular software updates can also introduce new features and improve existing functionalities.
- How to Keep the PLC Software Updated: Follow the manufacturer’s guidelines for updating the PLC software.
- The Importance of Regular Backups: Regularly back up your PLC programs to prevent data loss in case of system failure.
Environmental Considerations
The environment in which the PLC operates can significantly impact its performance.
- Ensuring Optimal Operating Conditions: Maintain the recommended temperature and humidity levels to prevent overheating or moisture damage.
- Dust and Debris Management: Keep the PLC and its surroundings clean to avoid dust accumulation, which can interfere with electronic components.
By following these maintenance tips, you can ensure that your Omron PLCs operate efficiently and reliably, minimizing downtime and extending their service life.
Troubleshooting Common Issues
Diagnostic Tools
Effective troubleshooting of Omron PLCs begins with the right diagnostic tools. These include software for monitoring and programming, such as CX-Programmer, and hardware tools for testing connections and signal integrity. Understanding how to use these tools is crucial in diagnosing and resolving issues efficiently.
Common Problems and Solutions
- Power Issues: Power-related problems often manifest as complete non-functionality or erratic behavior. Checking power supply connections, verifying input voltage levels, and inspecting fuses can resolve these issues.
- Communication Errors: Communication faults can be traced back to incorrect configurations, faulty cables, or incompatible protocols. Ensuring proper setup and inspecting physical connections often solves these problems.
- Input/Output Issues: Problems with inputs and outputs can include non-responsive sensors or actuators. Checking wiring, verifying configurations, and testing individual I/O points can be effective.
- Software and Programming Errors: Software glitches or programming mistakes can cause unexpected behavior. Regular software updates and thorough debugging of the PLC program are essential.
When to Seek Professional Help
Recognize situations where professional intervention is required, such as hardware failures, complex software issues, or when the problem persists despite basic troubleshooting.
Preventative Measures
Training and Documentation
- Importance of Staff Training: Well-trained personnel can prevent many issues through proper handling and quick identification of potential problems.
- Keeping Detailed Documentation: Maintain detailed records of configurations, modifications, and past issues for efficient troubleshooting.
Regular Audits and Updates
- Scheduling Regular System Audits: Periodically reviewing the entire PLC system can identify potential issues before they escalate.
- Keeping Systems Updated and Secure: Ensure that both hardware and software components are kept up-to-date with the latest versions and security patches.
Why is PLC Not Working?
When a PLC is not functioning, the issue could be due to a variety of factors. Common causes include power supply problems, such as incorrect voltage or failed power components; programming errors that disrupt operational logic; communication failures between the PLC and other devices; or physical damage to the PLC hardware. It is essential to systematically diagnose the issue, starting with basic checks like power supply and wiring, and then progressing to software and communication configurations.
What are the Common Errors in PLC?
Common errors in PLC systems often revolve around:
- Power Supply Issues: Inadequate power supply or disruptions.
- I/O Faults: Misconfigured, faulty, or damaged input/output modules.
- Communication Failures: Issues in network protocols or physical connections.
- Programming Errors: Logic errors or corruption in the PLC program.
- Hardware Malfunctions: Physical damage or wear and tear of PLC components.
How to Do PLC Maintenance?
PLC maintenance involves several key steps:
- Regular Inspections: Conduct visual inspections for physical damage and check all connections.
- Environmental Controls: Ensure the PLC is operating in a clean, dry, and temperature-controlled environment.
- Software Updates and Data Backups: Regularly update the PLC software and backup important program data.
- I/O Tests and Calibration: Regularly test and calibrate input/output modules to ensure accurate data processing.
- Documentation: Keep detailed maintenance logs for future reference.
What is the First Step in Troubleshooting a PLC?
The first step in troubleshooting a PLC is to check the status of the power supply and ensure that the PLC is receiving the correct voltage. This includes inspecting power connections, fuses, and indicators. Power issues are often the most straightforward problems and hence should be ruled out initially.
How Do I Check My PLC Error?
To check PLC errors:
- Examine Indicator Lights: Many PLCs have indicator lights that signal specific error types.
- Use Diagnostic Software: Connect to the PLC using diagnostic software to read error codes and detailed error messages.
- Check Program Logs: Review the PLC program logs for any anomalies or error messages logged during operation.
How Do You Test a PLC System?
Testing a PLC system involves:
- Simulating Inputs: Apply simulated inputs to the PLC and observe if the outputs behave as expected.
- Using Diagnostic Tools: Utilize built-in diagnostic tools or external software to conduct system checks and monitor performance.
- Load Testing: Apply operational loads to the system to ensure it can handle real-world conditions.
- Checking Communication Links: Verify that the PLC can communicate effectively with other networked devices.
- Manual Inspection: Physically inspect the PLC and associated hardware for any signs of damage or wear.
Conclusion
Regular maintenance and effective troubleshooting are pivotal in maximizing the efficiency and lifespan of Omron PLCs. This guide provides a foundational approach to maintaining and troubleshooting these systems.
If you need immediate technical support or are looking to purchase genuine OMRON industrial automation products, feel free to contact us at info@ikwoco.com. With over 30 million worth of product inventory, our team at ikwoco is dedicated to providing quick quotations, delivery, and technical support for OMRON products.