Navigating the landscape of network automation and establishing seamless communication between your Omron devices and Visual Basic (VB) over Ethernet can be a daunting task.
Yet, it remains an indispensable skill for those striving for optimal system performance.
Welcome to our comprehensive guide, a ‘Step-by-Step Guide to Flawless Omron Communication via Ethernet in VB’, where we unravel this seemingly complex process, providing a clear and concise roadmap for engineers and technicians alike.
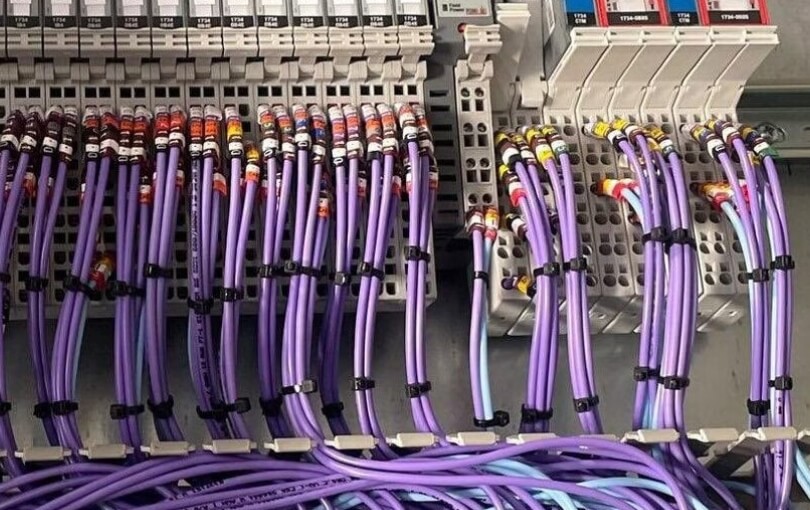
As practitioners in the field, you may initially find the task of integrating Omron devices over Ethernet using VB challenging, especially if you’re in the early stages of your career or new to this particular communication protocol.
Fear not, this article is crafted with the aim of decoding this process, transforming it into a digestible and manageable task.
This guide aims to serve as your navigational beacon, presenting each critical step in a logical, easy-to-follow manner.
We’ll shine a light on common stumbling blocks, dispense practical advice to make your endeavors less taxing and share field-tested strategies for achieving reliable and efficient communication.
Whether you’re seeking to extract the maximum potential from your existing systems or delving into uncharted waters, this guide caters to your needs.
So, let’s embark on this journey together toward mastering the art of flawless Omron communication in VB over Ethernet.
The Importance of Effective Omron Communication via Ethernet in VB
In today’s interconnected world, the role of automation in system operations cannot be overstated.
Particularly for engineers and technicians working with Omron PLC products, mastering the art of communication via Ethernet using Visual Basic (VB) is not merely a valuable skill—it’s a crucial one.
Omron PLCs are renowned for their robustness, reliability, and versatility, finding applications in a wide array of sectors from manufacturing to transportation.
However, the true power of these devices comes to life when they can ‘talk’ and ‘listen’ effectively in a network—primarily achieved through seamless, real-time communication over Ethernet.
Ethernet, as a widespread standard for wired networks, offers high-speed, reliable communication.
When combined with VB, a programming language praised for its ease of use and versatility, it opens up a world of possibilities.
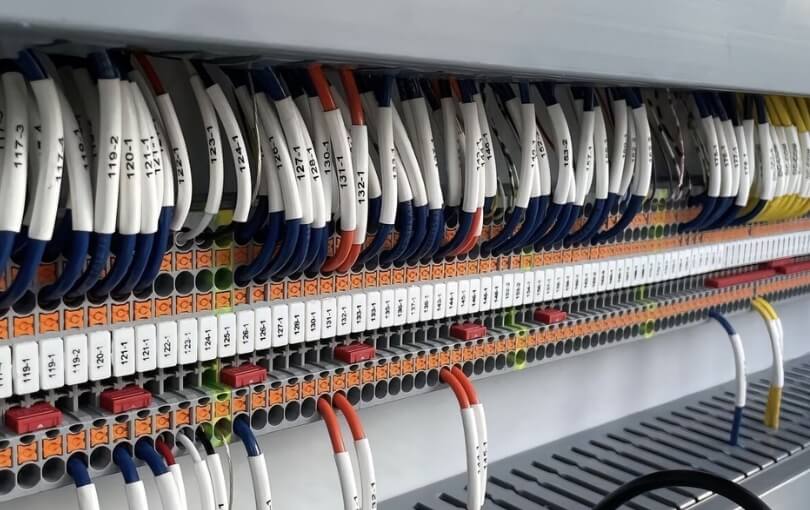
From overseeing production lines, and managing quality control, to running safety systems—these are but a few of the tasks that become far more streamlined and efficient.
Effective communication between your Omron PLC and VB over Ethernet allows for real-time monitoring, predictive maintenance, and quick troubleshooting.
It provides the basis for ‘smart’ operations—ones that are proactive rather than reactive.
By predicting equipment failures before they occur or spotting bottlenecks in the production line, operations can be optimized, and costly downtime can be minimized.
Moreover, VB plays a significant role in this process. It simplifies the task of writing programs that can effectively communicate with your Omron devices.
With its user-friendly syntax and a wide array of functions, VB allows you to create powerful, customized solutions tailored to your specific needs.
Therefore, understanding and implementing effective communication with Omron devices over Ethernet using VB is not just about leveraging technology—it’s about pushing the boundaries of efficiency, productivity, and innovation in any system operation.
Indeed, it is a keystone of modern automation and a vital tool in the engineer’s and technician’s kit.
A Brief Introduction to Omron PLC Products
Omron Programmable Logic Controllers (PLCs) are the workhorses of the automation industry, with a reputation for robustness and reliability.
These devices are designed to handle a wide array of tasks in various sectors, including manufacturing, logistics, and infrastructure. With a range of PLCs suited for different applications, from compact and cost-effective units for simple control systems to powerful modular PLCs for complex processes, Omron is a trusted name in the industry.
These PLCs function as the brains of an automated system, processing inputs from various sensors and devices, and directing the outputs to drive mechanisms, such as motors, valves, and lights.
But their potential is fully unlocked when they can communicate effectively within a network, and this is where Ethernet and VB come into play.
Basics of VB and Its Use in Automation
Visual Basic (VB) is a programming language developed by Microsoft, widely recognized for its simplicity and intuitiveness.
Its user-friendly nature makes it an excellent choice for programming tasks in automation, including interfacing with PLCs.
The power of VB lies in its ability to create Windows-based applications quickly, and its support for COM (Component Object Model) technologies, which allow seamless integration with other automation tools and technologies.
From creating user interfaces for data display to writing complex control logic, VB provides a versatile platform for automation engineers to create customized solutions tailored to their unique requirements.
Introduction to Ethernet and Its Role in Communication
Ethernet is a networking technology that has become a standard for wired communication networks.
It connects devices on a local area network (LAN), such as computers, PLCs, and other hardware, enabling them to communicate and share data.
In the context of automation, Ethernet plays a pivotal role in achieving real-time, reliable, and high-speed communication between devices.
Unlike traditional serial communication, Ethernet allows data exchange at much higher speeds and over longer distances, making it ideal for modern, large-scale industrial applications.
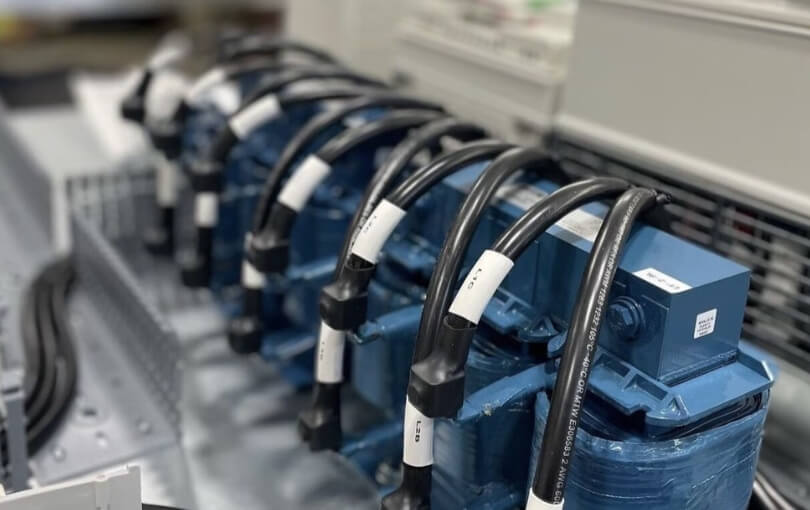
When a PLC, such as an Omron device, is connected via Ethernet, it can communicate and share data with other devices in the network, enabling centralized control and monitoring.
This interconnectivity is a cornerstone of Industry 4.0, underpinning technologies such as the Internet of Things (IoT) and enabling the creation of ‘smart’ factories and infrastructure.
Together, Omron PLCs, VB, and Ethernet form a powerful trio, enabling the creation of sophisticated, efficient, and intelligent automation systems.
In the following sections, we will explore how to harness these technologies to establish effective communication with Omron devices over Ethernet using VB.
Hardware Requirements
Setting up effective communication with Omron PLCs via Ethernet involves several hardware elements.
The first and foremost is, of course, an Omron PLC. Whether you’re using a compact or a modular PLC will depend on the complexity of your application.
Secondly, you’ll need a computer with an Ethernet port for connecting to the PLC. While many modern computers come equipped with this, in some cases, an additional Ethernet card may be necessary.
Finally, a standard Ethernet cable is required for the physical connection between the PLC and the computer. Remember to choose a high-quality cable that suits your environment and meets the distance requirements between your PLC and computer.
Software Prerequisites
On the software front, a couple of components are crucial for setting up Omron communication via Ethernet in VB.
The first is the VB development environment, typically Visual Studio, which allows you to write, test, and debug your VB code.
Secondly, you’ll need the relevant Omron drivers and libraries that allow VB to communicate with the PLC.
These drivers, like the FinsGateway or CX-Server, are usually provided by Omron and can be installed on your computer.
Configuring Your Omron Device and VB Environment
Once you have your hardware and software sorted, the next step is configuration.
On the Omron PLC, you’ll need to set the IP address, subnet mask, and default gateway to match your Ethernet network settings.
This ensures that your PLC can communicate effectively with other devices on the network.
On the VB side, ensure that your project references the necessary Omron libraries. This allows you to utilize pre-built functions and classes for communication with the PLC.
Finally, test the connection between your computer and the PLC.
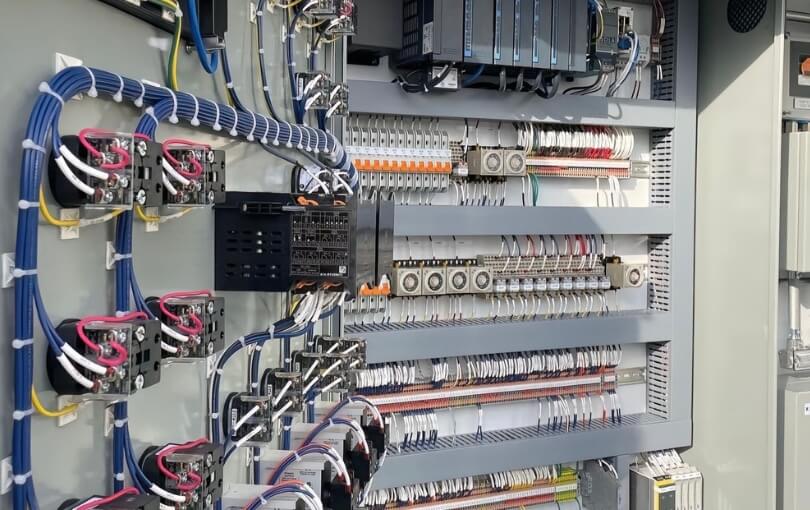
This can typically be done using a simple ‘ping’ command in the command prompt on your computer, or through a connectivity test in your Omron software.
If the PLC responds correctly, you’ve successfully set up your hardware and software for effective Omron communication via Ethernet in VB.
This sets the foundation for writing the VB code that will control and monitor your Omron PLC.
Remember, the devil is in the details when it comes to this setup process, and it’s essential to ensure everything is correctly configured to achieve smooth, error-free communication.
Step 1: Establishing the Connection
The first step in setting up communication with your Omron PLC is establishing a connection.
This involves writing VB code that instructs your computer to connect to the PLC over Ethernet.
Using the relevant libraries and drivers installed earlier, you’ll typically specify the PLC’s IP address and the communication protocol (in this case, Ethernet).
Once the connection request is sent, if the PLC accepts the connection and everything is set up correctly, your VB program will now have a communication link with the PLC.
It’s recommended to include checks in your code to ensure the connection is successfully established before proceeding.
Step 2: Sending and Receiving Data
Once your connection is established, you can start sending and receiving data. In VB, you’ll write functions or methods to write data to the PLC or read data from it.
The nature of this data will depend on your application – you may be sending control commands, writing values to PLC registers, or reading sensor data, among other things.
Remember, data sent and received will typically be in a specific format or protocol understood by the PLC and your VB program. Ensure your code correctly formats the data before sending and correctly interprets received data.
Step 3: Interpreting Responses
When you read data from the PLC, it will typically be in response to a query or command sent from your VB program.
Interpreting this response correctly is critical to ensure your program behaves as expected.
This might involve checking status flags or reading values from specific registers.
For instance, a sensor might send a specific value when a limit is exceeded, or the PLC might set a flag when a certain condition is met. Your VB program should be able to interpret these responses correctly and take appropriate action.
Step 4: Error Detection and Troubleshooting
No matter how meticulously you prepare, errors can and will occur.
The final step, therefore, involves adding error detection and troubleshooting capabilities to your VB program.
This could involve checking for timeouts (when the PLC doesn’t respond within a certain time), handling unexpected responses, or dealing with connection errors.
When such an error is detected, your program should ideally log the error, attempt to rectify it if possible, or alert the user if necessary.
While this might seem daunting, remember that with every error comes a learning opportunity.
Over time, you’ll learn to anticipate common issues and build robust VB programs that can effectively communicate with your Omron PLCs over Ethernet.
Most Common Issues When Setting Up Communication
Setting up communication between an Omron PLC and a computer using VB over Ethernet can sometimes be a bumpy ride. Here are a few common issues that you might encounter:
Incorrect Network Settings: One of the most common issues is improper network configuration. This could be mismatched IP addresses, subnet masks, or gateway settings between the PLC and the computer.
Firewall Issues: Sometimes, the communication might be blocked by the firewall settings on the computer. If you’re sure the network settings are correct, but communication isn’t happening, the firewall might be the culprit.
Incorrect Data Format: Data sent to the PLC or received from it needs to follow a specific format. Errors can occur if this data is not formatted correctly.
Timeout Errors: These errors occur when the PLC does not respond within a set period. This could be due to network latency, PLC being busy with other tasks, or problems in the communication link.
Best Practices to Avoid Common Pitfalls
While these issues can be frustrating, here are some best practices that can help you avoid these common pitfalls:
Double-Check Network Settings: Before you begin, ensure that your PLC’s network settings match with those of your computer. This includes the IP address, subnet mask, and gateway.
Manage Your Firewall: If you’re having trouble establishing communication, consider checking your firewall settings. In some cases, you might need to create an exception for your VB application or Omron software.
Use Proper Data Formatting: Always ensure that the data you send to the PLC or receive from it is correctly formatted. Utilise the libraries provided by Omron to help with this.
Implement Error Handling: Building robust error handling in your VB code can save you a lot of trouble. This includes handling timeout errors, checking the status of the communication link before sending or receiving data, and logging errors for future troubleshooting.
Remember, setting up communication with a PLC is a complex task, and problems are part of the process. But with these best practices, you’ll be well equipped to handle any issues that come your way.
Tips to Make the Process More Efficient
Plan Ahead: Have a clear plan of what you want to achieve with your Omron PLC and VB program. Understand what data needs to be exchanged, how often, and how the data should be processed. This can greatly streamline the coding process.
Leverage Omron Libraries: Make use of the libraries provided by Omron. They have pre-built functions that can save you time and reduce the chances of errors in your code.
Test in Phases: Test your code in stages rather than waiting to test everything at the end. This can help you identify and fix errors sooner and can make the overall process more manageable.
Document Your Code: Properly documenting your code can save you a lot of time, especially when troubleshooting. This includes adding comments in your code to explain what each section does and maintaining a separate document that explains your overall program structure.
Maintenance and Updates for Your System
Maintaining your system and keeping it updated is just as important as setting it up. Here are some tips:
Keep Your Software Updated: Ensure that your VB environment and Omron software and drivers are always up-to-date. Software updates often contain bug fixes and improvements that can make your system more stable and efficient.
Monitor Your System: Regularly monitor your system for any issues. This includes not just looking for errors in your VB program, but also checking the status of your PLC and network connection. This can help you catch and fix issues before they become serious problems.
Regular Backups: Make sure to back up your VB code and PLC program regularly. This can save you a lot of trouble in case something goes wrong.
Scheduled Maintenance: Regularly scheduled maintenance of your hardware can prevent many problems. This includes cleaning your PLC and computer, checking for any physical damage, and replacing any faulty components.
Remember, efficiency and maintenance are ongoing processes. By continually looking for ways to improve your system and keep it in good health, you can ensure that your Omron PLC and VB program continue to communicate effectively over Ethernet for a long time.
Real-world Example of Effective Omron Communication via Ethernet in VB
Imagine an automated production line in a large manufacturing facility, with a complex network of conveyors, robotic arms, sensors, and other devices, all orchestrated by an Omron PLC.
To enhance the operational efficiency and flexibility of the system, the facility decided to develop a custom VB application.
This application connects to the Omron PLC over Ethernet and allows the operators to monitor and control the production line in real-time from a centralized computer.
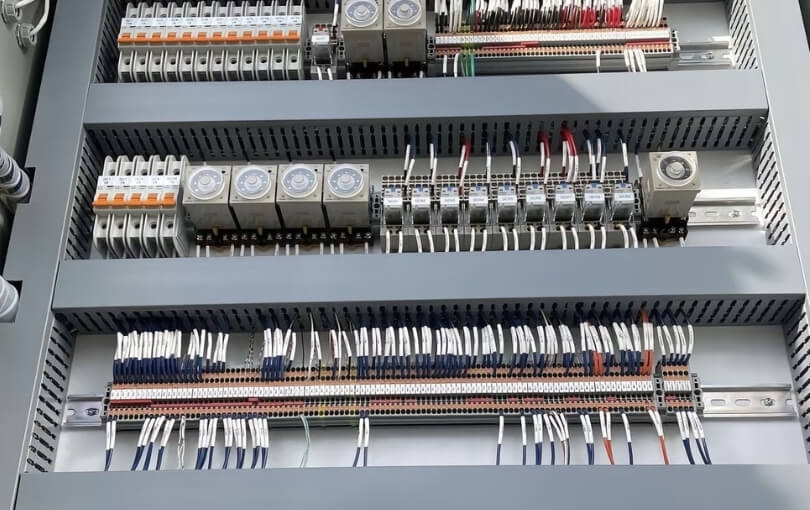
The VB application displays real-time sensor readings and system status on a user-friendly interface, logs production data for future analysis, and allows operators to adjust the system parameters on the fly.
The application communicates with the PLC by sending and receiving data packets over Ethernet, utilizing the communication functions provided by the Omron libraries.
This system has not only increased the production line’s efficiency but also made troubleshooting easier and improved the operators’ ability to react to changes in the production requirements, demonstrating the value of effective Omron communication via Ethernet in VB.
Lessons Learned and Tips from the Field
Embrace Flexibility: The real world is always changing, and so too are the demands on your automated systems. Being able to adjust system parameters on the fly, as in the above example, can provide a great deal of operational flexibility.
Test, Test, Test: Systems rarely work perfectly the first time. Always test your system thoroughly, and in as many different scenarios as you can think of, before putting it into operation.
Communication is Key: Keep an open line of communication with all the stakeholders involved in your project. This includes the operators, maintenance staff, and management. Their feedback can often provide invaluable insights into how to improve your system.
Never Stop Learning: Technologies are always advancing. Stay up-to-date with the latest developments in VB, Omron PLCs, and Ethernet technology to ensure that your system continues to meet the demands of the modern world.
Remember, the principles discussed in this blog post aren’t just theoretical. They’re proven strategies used by engineers around the world to unlock the potential of their Omron PLCs through effective communication via Ethernet in VB.
The Importance of Mastering This Skill for the Future
Mastering the art of effective communication between an Omron PLC and a VB application over Ethernet is more than just a handy skill – it’s a cornerstone for any engineer or technician working in an increasingly automated world.
With industries continually striving for increased efficiency and reliability, this skill will not only make you more proficient in your current role but also more valuable in the job market.
Moreover, as industries move towards Industry 4.0 – the next revolution that entails interconnectivity, automation, machine learning, and real-time data – having a profound understanding of PLC communication will undoubtedly become a necessity.
Encouragement for Further Learning and Development
This article is just the beginning. I would strongly encourage you to continue to explore and learn.
Delve deeper into each of the steps we’ve discussed, experiment with your code, try different configurations, and most importantly, don’t be afraid to make mistakes. Each error is a learning opportunity and a step closer to mastery.
We would love for every learner to have an in-depth conversation with ikwoco’s technical experts and learn from each other!
The more you learn and practice, the more adept you’ll become at not only communicating with Omron PLCs via Ethernet in VB, but also in navigating the broader landscape of automation technology.
Always remember, in the field of technology, the best way to predict the future is to invent it. Happy learning!